Bosch Advanced Ceramics has reported the successful Additive Manufacturing of a ceramic insulating sleeve for a laparoscopic tool used in minimally invasive surgery. A standout achievement in the project was said to be the ability to manufacture 1,400 parts in a single batch, demonstrating both the precision and scalability of the process.
The team started with the challenge of producing a component with a maximum external diameter of 1.3 mm and a wall thickness of just 90 µm. The part’s small size and complexity were critical for its function as an electrical insulator within the medical device.
Using Lithography-based Ceramic Manufacturing (LCM) technology, a form of Vat Photopolymerisation Additive Manufacturing from Lithoz GmbH in Vienna, Austria, Bosch Advanced Ceramics was able to ensure exceptional precision and design flexibility. This level of detail would be impossible with conventional manufacturing processes.
The development process for the insulating sleeve required several design iterations to balance structural integrity with electrical insulation properties. The AM technology used allowed Bosch Advanced Ceramics to make rapid adjustments to the design and process parameters, enabling them to fine-tune the manufacturing approach. Each version of the part underwent rigorous testing, and four iterations were tested to achieve the optimal wall thickness and external diameter.
By leveraging the 40 µm resolution of Lithoz’s CeraFab machine, Bosch Advanced Ceramics could consistently produce parts with the required 90 µm wall thickness. This was a key factor in the component’s performance, as it had to fit within the confines of a laparoscopic tool and provide insulation between two conductive components.
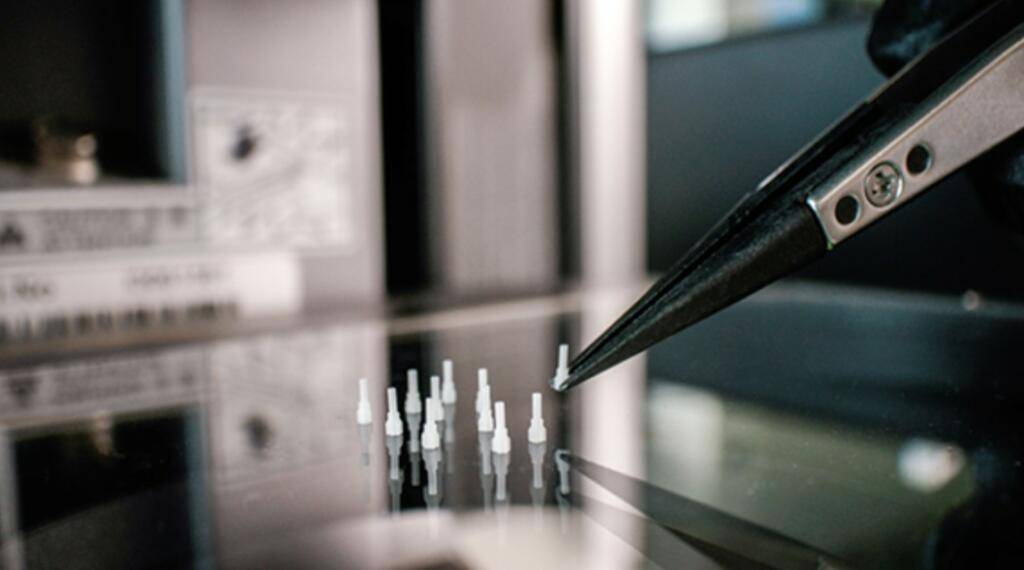
Bosch Advanced Ceramics used LithaLox 360 alumina, a material offering excellent thermal resistance, chemical stability, and electrical insulation. These properties were crucial for the component’s performance in the demanding conditions of surgical sterilisation and use.
Following a successful sample phase, Bosch Advanced Ceramics began scaling up production. The ability to produce 1,400 parts per batch on a single build plate allowed Bosch Advanced Ceramics to rapidly meet the customer’s demand, set at 20,000 parts per year.
A critical factor in this achievement was also reported to be Bosch Advanced Ceramics’ proprietary cleaning process, which allowed for gentle and effective handling of the fragile green parts post-build. This automated process ensured that excess material was removed without damaging the delicate structures, maintaining the quality and consistency of each batch.