In Short: CHROMOS Group AG, an innovative solutions provider in the industrial sector, shared a case study of their client, designunity.ch which they held for dAHLer (autotuning bureau). The end-client (dAHLer) upgraded BMW M240i and BMW G80 series, enhancing the aerodynamics of the cars by adding front splitter lip to the bumper. The project was held with the help of 3D technologies, where Calibry scanner was used to digitize the car front.
The aim: To make hi-res model of a bumper that later could be used for CAD design. The investment cost of the project should be kept low.
Instruments: Calibry 3D scanner, Calibry nest software, Rhino software, 3D printer
Achieved results: With the help of 3D-technologies, solutions were quickly found to best meet the customer’s requirements: high quality scan data suitable for subsequent reverse engineering while keeping costs low through cost optimization. For BMW m240i series the upgrade was already successfully implemented. The G80 series is currently in line.
dAHLer, an autotuning company headquarted in Switzerland, has been the source of BMW tuning parts and accessories since 1996. dAHLer offers a wide range of tuning products for BMW fans: coil-over suspensions, lowering kits, performance exhaust systems, forged wheels, interior parts and much more. dAHLer’s upgrades are all about speed and power. As stated on their website, the goal is to “transform your stock car into a true Ultimate Driving machine”.
When we talk about speed maximization aerodynamic drag becomes a key problem to consider. As part of their upgrade strategy dAHLer offers body parts such as front splitters, rear wings, side skirts, rear diffusers and mirror caps that enable the car to cut through the air smoothly.
The latest two upgrades that dAHLer held were for BMW M240i and BMW G80 series, where Calibry 3D scanner was used to make front splitter lip.
The first part of the project, the scanning, was held at dAHLer’s showroom. A matting spray was applied to the front bumper of the vehicle. This was enough for the Calibry 3D scanner to capture the geometry in high resolution. No markers were needed. The scanning lasted for about 40 minutes starting from unpacking the scanner and preparing the workplace.
There were made multiple single scans of the vehicle front. Data post-processing with merging the scans into one single model took approximately 1.5 hour. After the model was completed in Calibry Nest, the second part of the project started – CAD modelling.
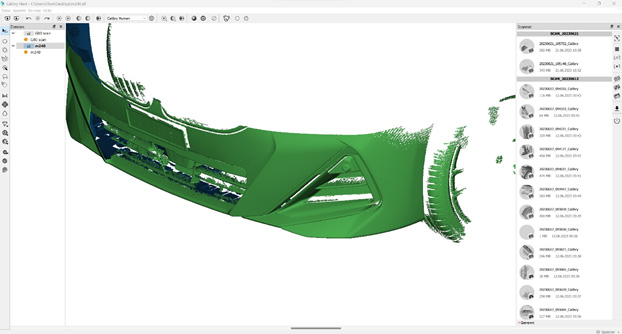
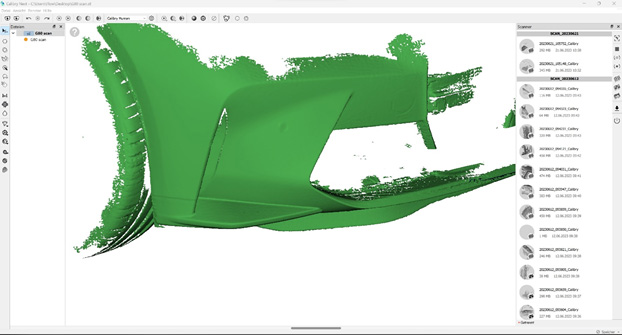
The design was done in Rhino software and involved numerous stages of edits and adjustments. In the final phase of the design, 2-3 of the most successful works were selected. These prototypes were 3D-printed to “try on” the car and choose the most favorable variant. All of the designer’s solutions looked good on the computer screen, but dAHLer wanted to choose the one that would look best in real life.
After a careful selection of prototypes, the final version was spraypainted and attached to the car for press release images to be taken.
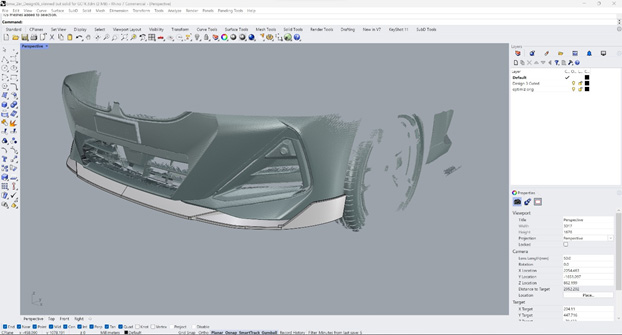
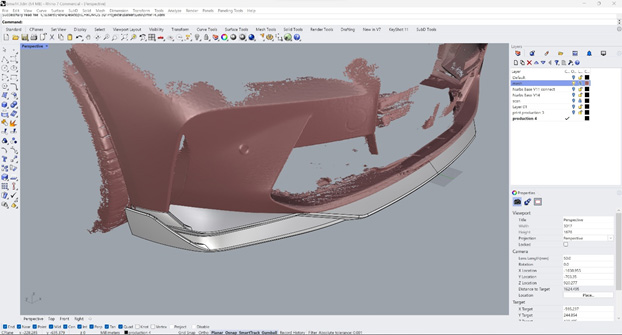
After final approval of the design and mounting fittings, the CAD data was sent to a Carbon parts manufacturer, with a targeted production volume of approximately 30 parts annually.
BMW M240i has already a carbon front splitter lip, while the M4 model temporarily has a 3D-printed one.
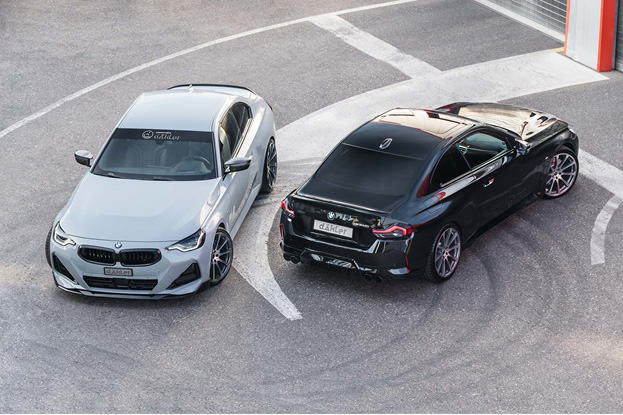
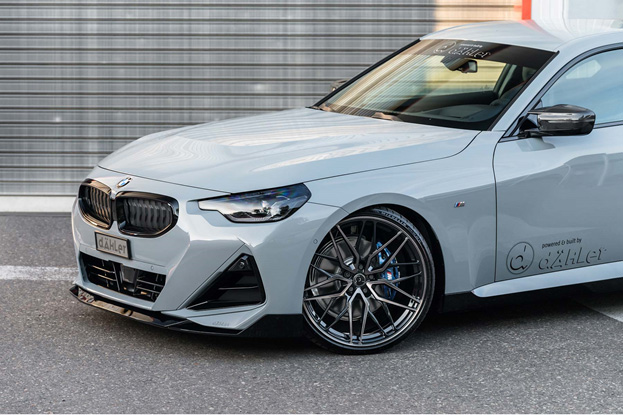
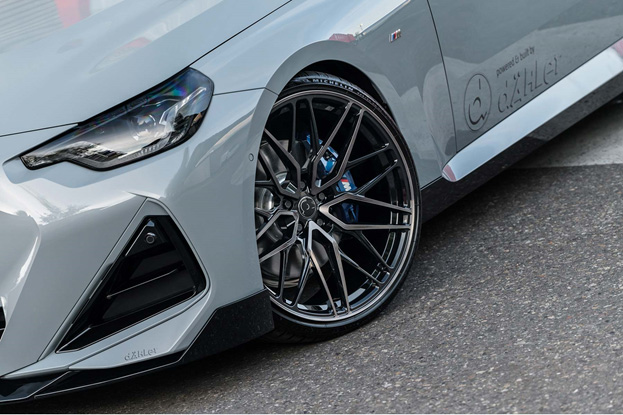
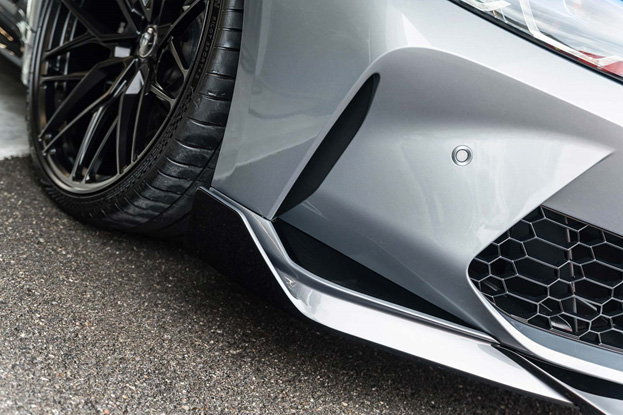
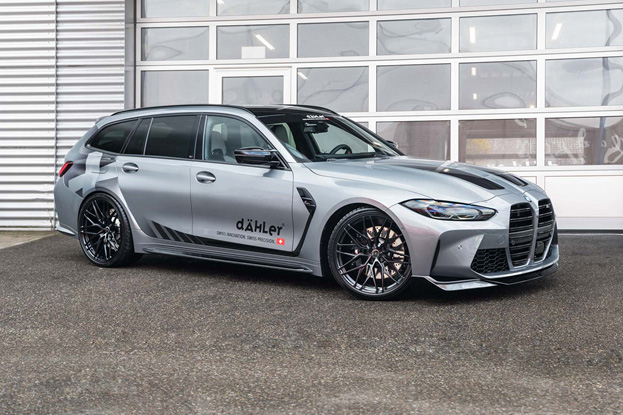
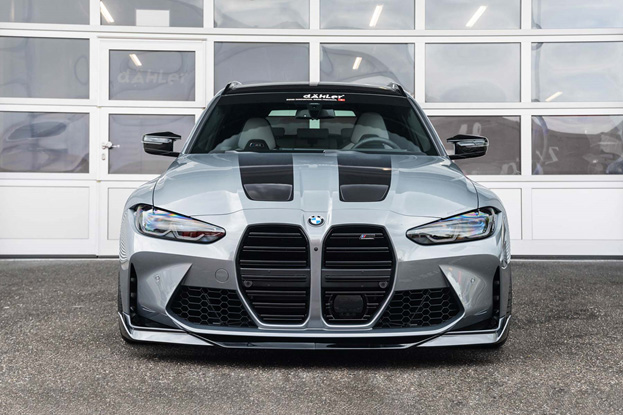
According to the project participants Calibry was picked “due to its ease of use, precision, fantastic scan software, portability, sturdiness and last but not least the investment cost, compared to other systems.”
High-res scanners appeared to be expensive which increased the production costs beyond planned. Most of the affordable scanners didn’t meet the quality requirements. Calibry was chosen for optimal value for money.
Subscribe to AM Chronicle Newsletter to stay connected: https://bit.ly/3fBZ1mP
Follow us on LinkedIn: https://bit.ly/3IjhrFq
Visit for more interesting content on additive manufacturing: https://amchronicle.com